Incessant technological challenges.
Discover innovation in the
manufacture of ring gears!
Birth of the Benda Method
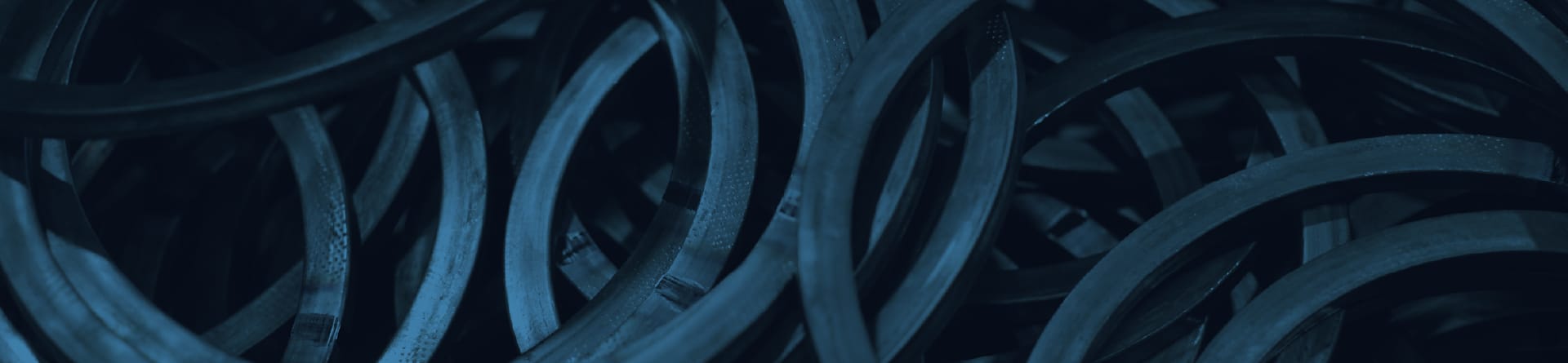
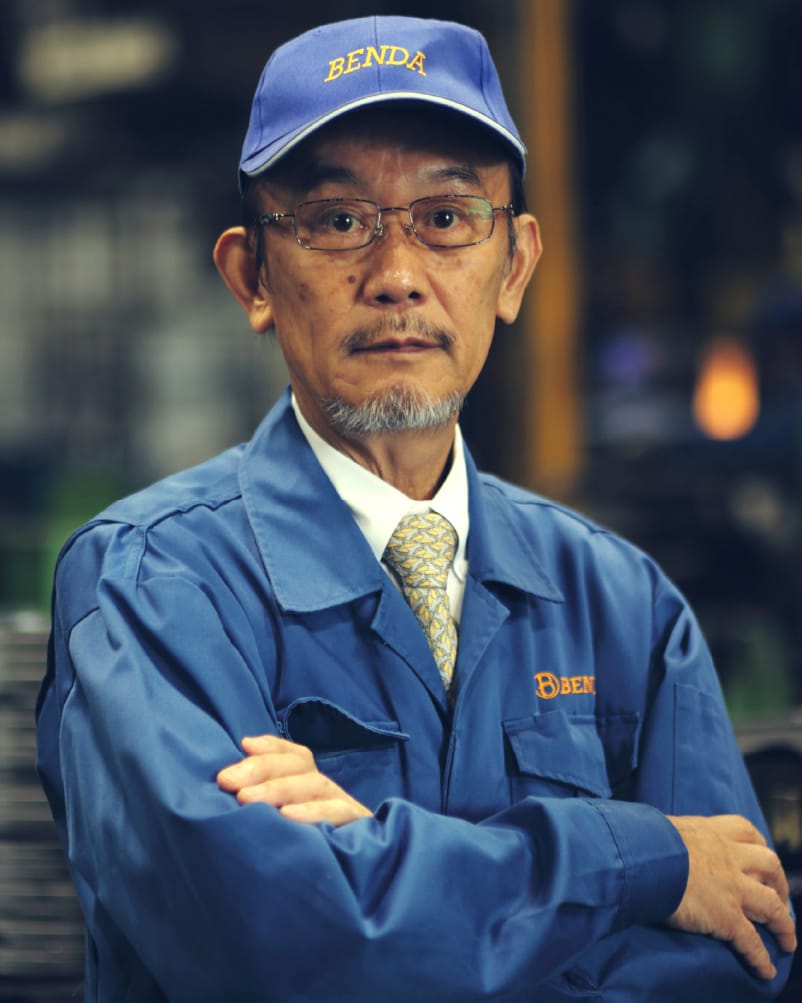
- Former advisor
- Koji Yashiro
"Bending Steel."The initial spark that ignited founder Kazuyoshi Yashiro's interest in bending steel materials came from a European equipment expo. Around 1959, during a European inspection tour organized by the Hiroshima Chamber of Commerce and Industry, he visited a local equipment expo and saw an angle bender. He showed a strong interest in the machine used for cold bending and took photos of it.
Later, when Yashiro Machinery & Materials Trading went bankrupt and he started Benda Kogyo, he used the name "Benda" (derived from the English word "bend") as the company name, reflecting his extraordinary determination to rebuild through bending. True to the word "we will bend the world's iron," Benda Kogyo took on the challenge of bending to meet various demands. The experience of widely handling cold bending and general bending for dam floodgate, rotating observation restaurants, pipelines, bridge pier guide rings, tunnel supports, pedestrian bridges, etc. became the foundation for developing the Benda method.
Why? The origin of the project
The impetus was a request from an automobile manufacturer. They wanted to know if we could mass-produce ring gears by cold bending, and Kazuyoshi came up with the idea of cold bending square steel and welding it.
First, round steel bars were rolled into square cross-sections and then rolled into spirals. At this time, due to the difference in elongation between the outer and inner diameters of the spirally wound steel, the cross-section became trapezoidal, and there was a problem that it could not be wound uniformly. He immediately devised a special-shaped material using inverse calculation. When the spirally wound steel was cut vertically on the side, a large number of cut rings were produced. Welding the cut surfaces together would create rings, but simply welding and joining the steel would not provide sufficient welding strength, and the rings would not be perfectly circular.
After much trial and error to solve this problem, we arrived at a method of overlapping the ends when cutting the rings. By utilizing the elastic stress of the metal, the spirally wound steel is passed through a mandrel slightly larger than the inner diameter of the spiral, and the ring is pushed out before cutting. When the mandrel is removed, the once expanded ring returns to its original shape, and the inner diameter becomes slightly smaller. The ends slightly overlap, so they are welded together while melting to create a flat ring.
Kazuyoshi, who continued to think about this, came up with this method at 2 o'clock in the middle of the night while sleeping, inspired by a hint in a dream. Koji and Yukio, who were shaken awake, took notes while rubbing their sleepy eyes. The next morning, Kazuyoshi consulted with a jig manufacturer and had the device made. The method devised by Kazuyoshi over six months from the request was finally adopted by automobile manufacturers other than the original requester, and mass production was decided.
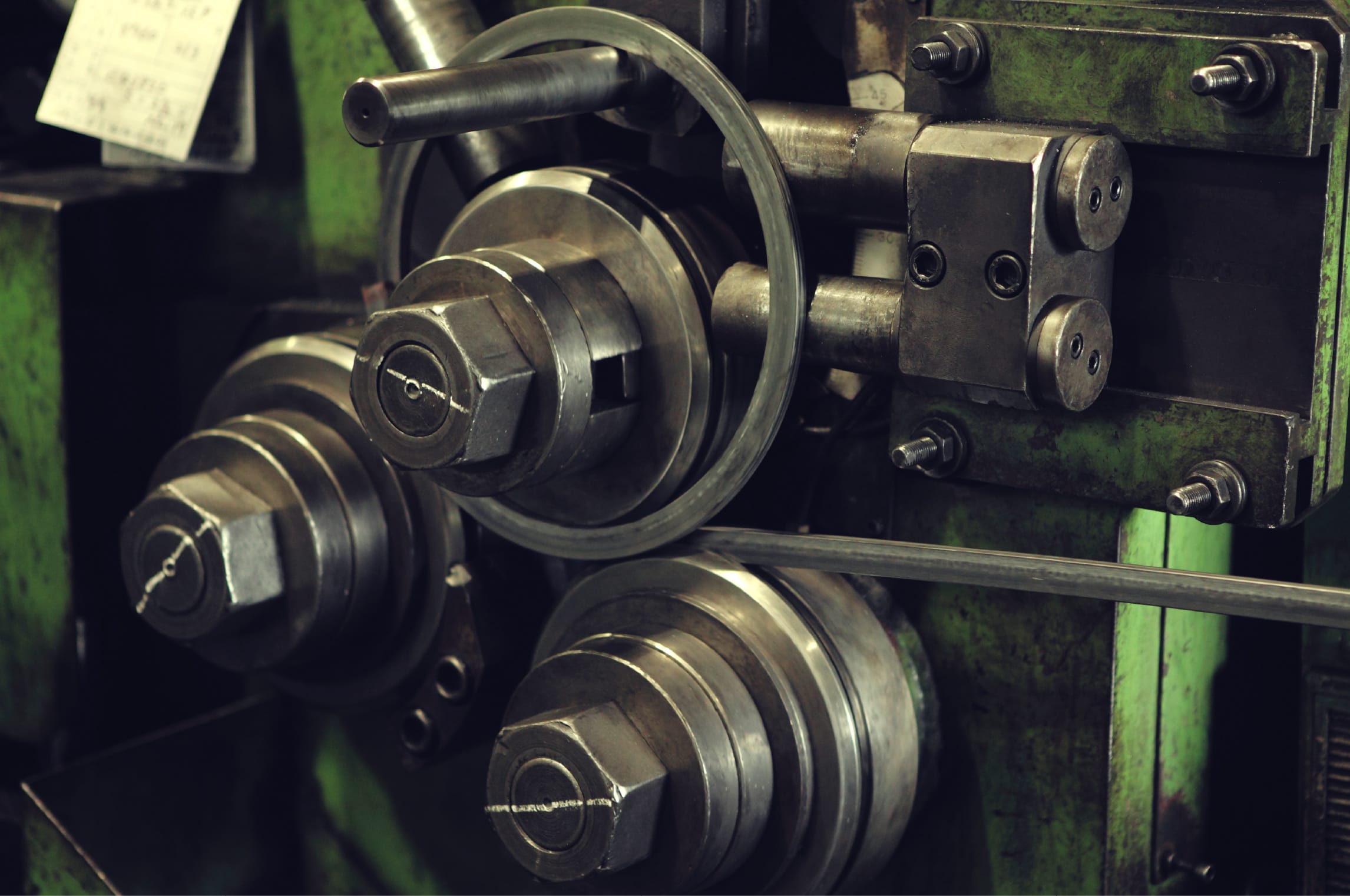
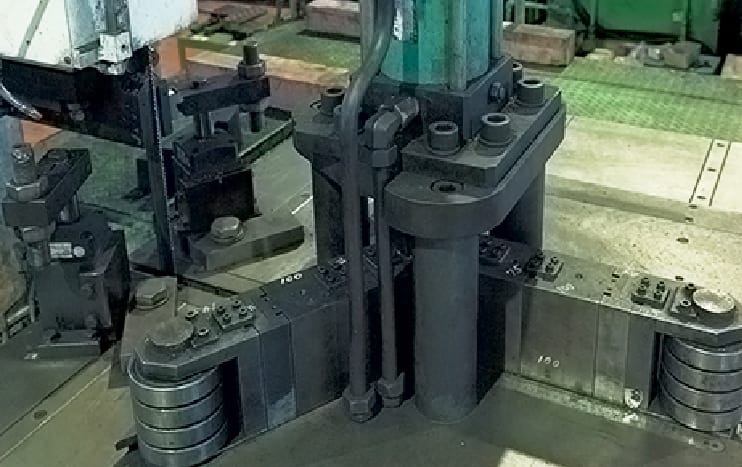
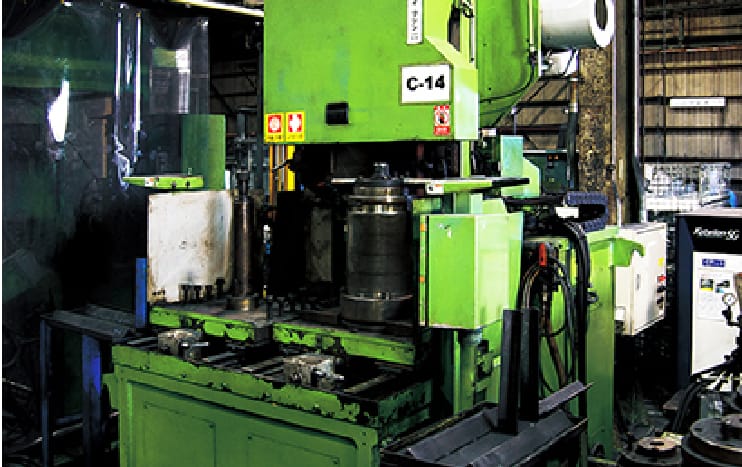
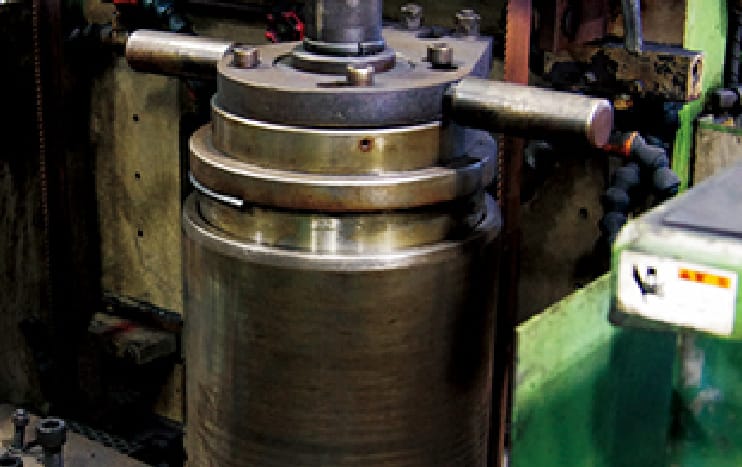
How? Product development challenges
With the start of mass production, we designed in-house equipment such as bending machines, cutting machines, and trimming machines necessary for the process of forming rings. Equipment and machinery are not finished once they are completed. Productivity is increased only when they are operated and mastered. Koji repeatedly made mistakes, collected vast amounts of data, and explored adjustment methods to improve the precision of the machines. Thanks to this data, we were able to complete an equation that could handle various bending conditions. Koji has also been involved in the automation and standardization of equipment. Because he had 15 to 30 years of experience in manual cutting, welding, and handwork, he constantly thought about how to eliminate waste and work efficiently, and worked to improve and standardize equipment.
For example, the new method cutting machine developed at the head office factory in November 2007 simultaneously cuts two different sizes of coil materials. By stacking coil materials in four layers on each of the two cutting jig shafts and cutting the two types simultaneously, we achieved a 200% increase in productivity. The large cutting machine also became jig-free with the new method, resulting in significant cost reductions. At Benda Sunkwang, Representative Director Kim Jung-han developed a semi-automatic welding device. His achievements should not be forgotten either. He automated manual welding that was 100% dependent on human work. This improved the issues of variations in productivity and quality due to the skill of the worker, and the heavy workload, and improved both product production efficiency and quality.
The Benda method has been further refined in the process of mass production and is a method established by the culmination of various innovations. When Mamoru Oshika developed the Benda method, he struggled with the bending process. When attempting to bend rolled materials and wind them spirally, they would stretch like springs. After much trial and error to prevent this spring-like behavior, he arrived at the solution of level-adjusting washers. By using the stress when bending iron and simply inserting these washers during the bending process, it was possible to prevent them from becoming spring-like.
This is how the "Oshika washer" was born. While Oshika, who immediately puts his ideas into shape, Takashi Yamane (former Technical Advisor), who is good at calculations and immediately puts dimensions into drawings, says, "If you have the ability to execute your ideas, you will always see something." He has been designing jigs according to the equipment under Kazuyoshi's orders, but later he was also involved in the development of equipment that can be processed without jigs. In the Benda method, he says, "The first process is very important. If the previous process is not done properly, it will affect the next process.
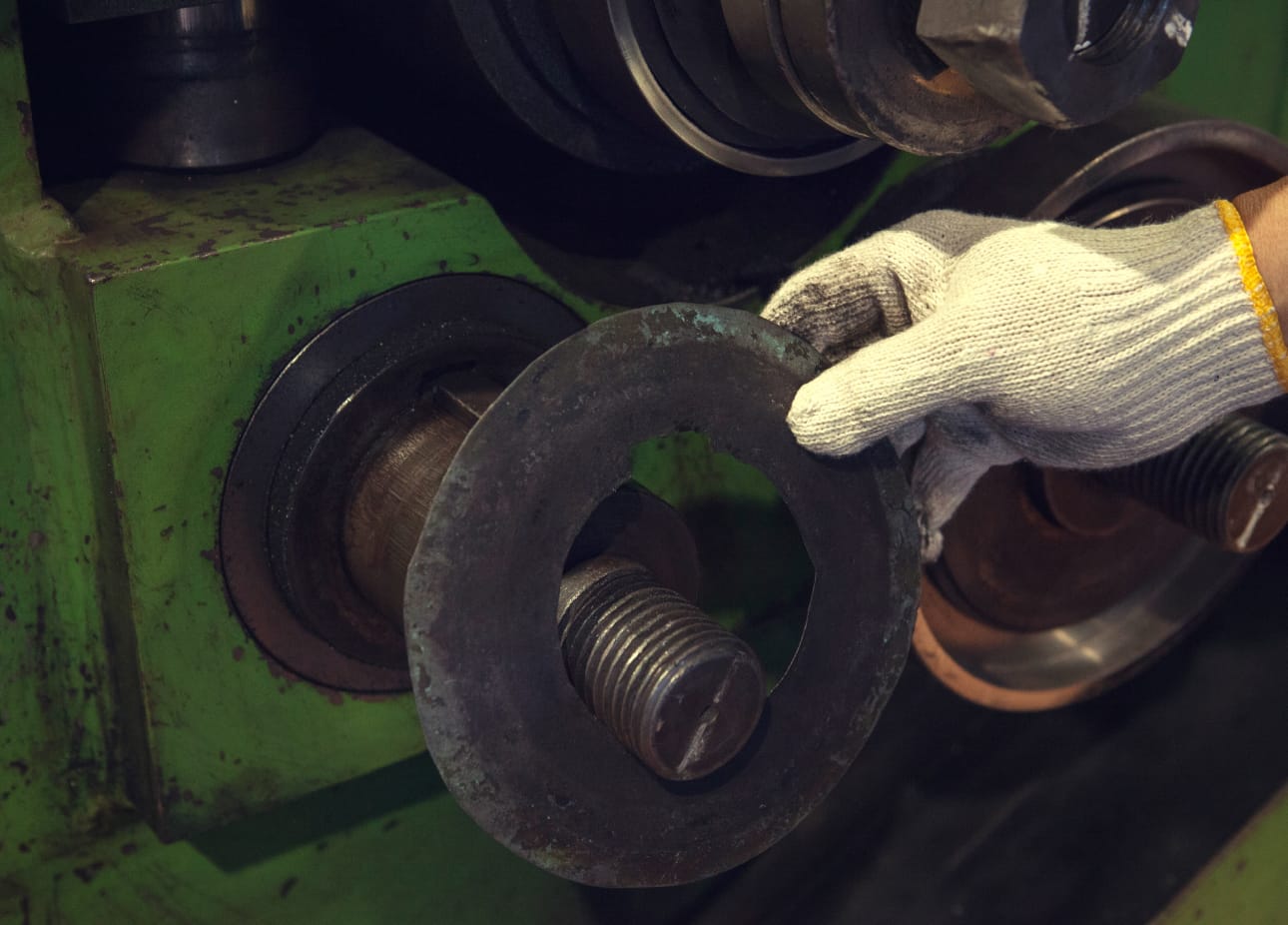
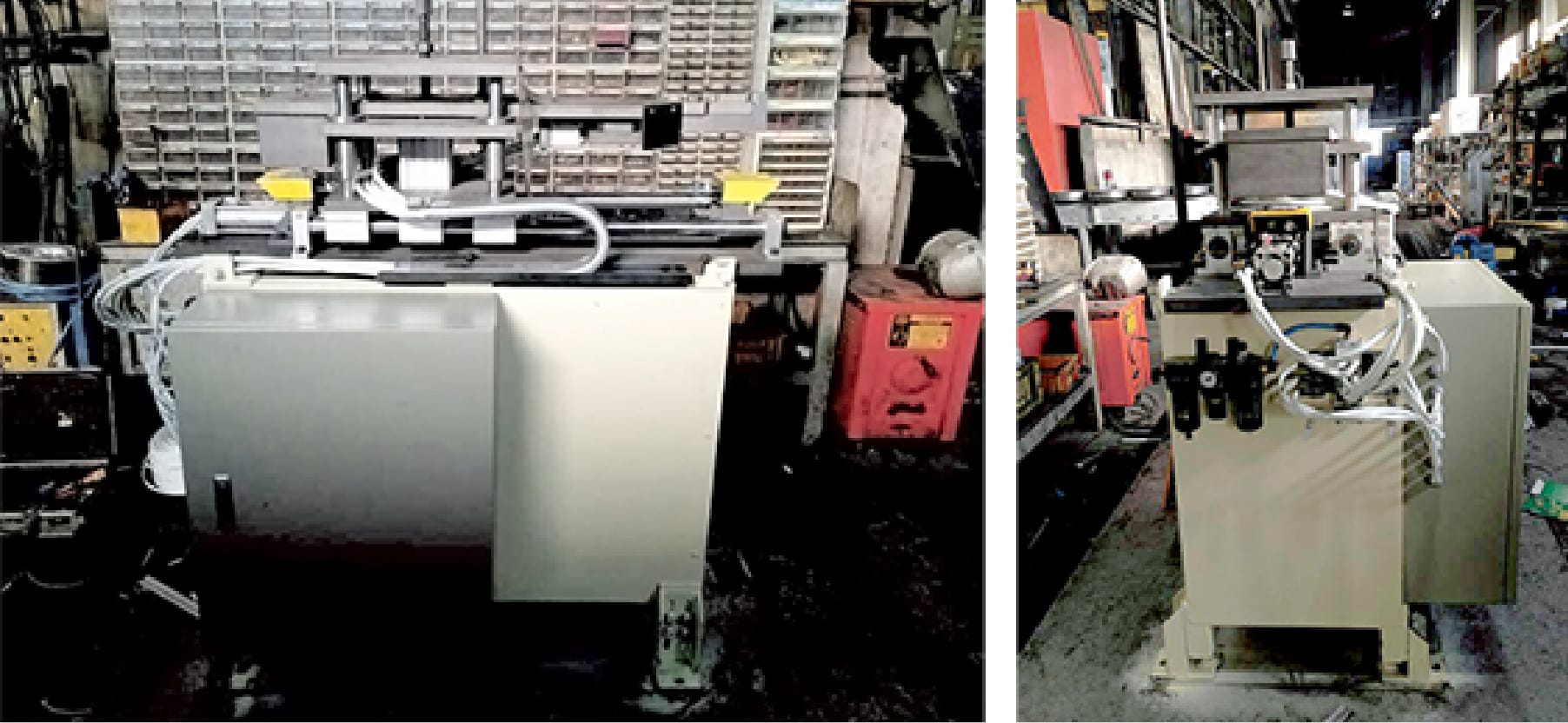
Review
What should be passed down is technology and spirit
The Bend method is described by its inventor, Kazuyoshi, as "a technology that cannot be easily imitated even after the patent expires. Its uniqueness has been further refined through daily improvements and enhancements by the artisans of Benda Kogyo and its overseas groups. Truly, 'the Benda method was not built in a day.' Initially, the process was manual, using hand-operated equipment, but through constant engagement with machinery and an unwavering interest in manufacturing technology, efficiency and improvements have been achieved. To pass on the Bender method overseas, Koji, Oshika, and Yamane have traveled to bases in Korea, Qingdao, and India, continuing to provide technical guidance. Kouji recalls overcoming health issues due to water and food in India while still conducting training. What should be passed on is not only the technology, but also the spirit of manufacturing that pursues possibilities together, without giving up in the midst of repeated failures. As Koji says, 'There is no end to improvement,' if we continue to make efforts and devise ways to improve without being satisfied with the current situation, new technologies and possibilities will be born, bringing great leaps to the Benda Group.
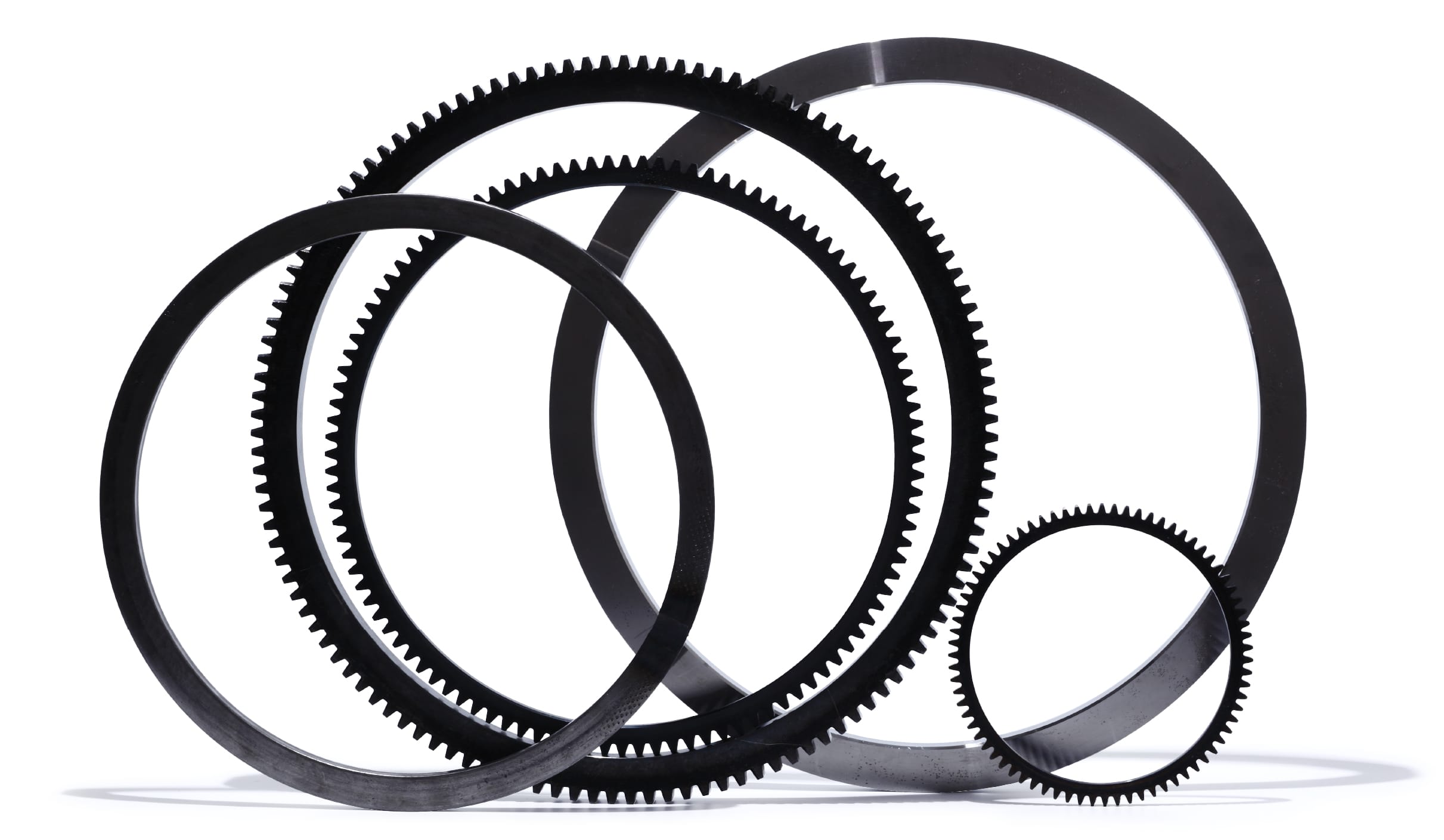