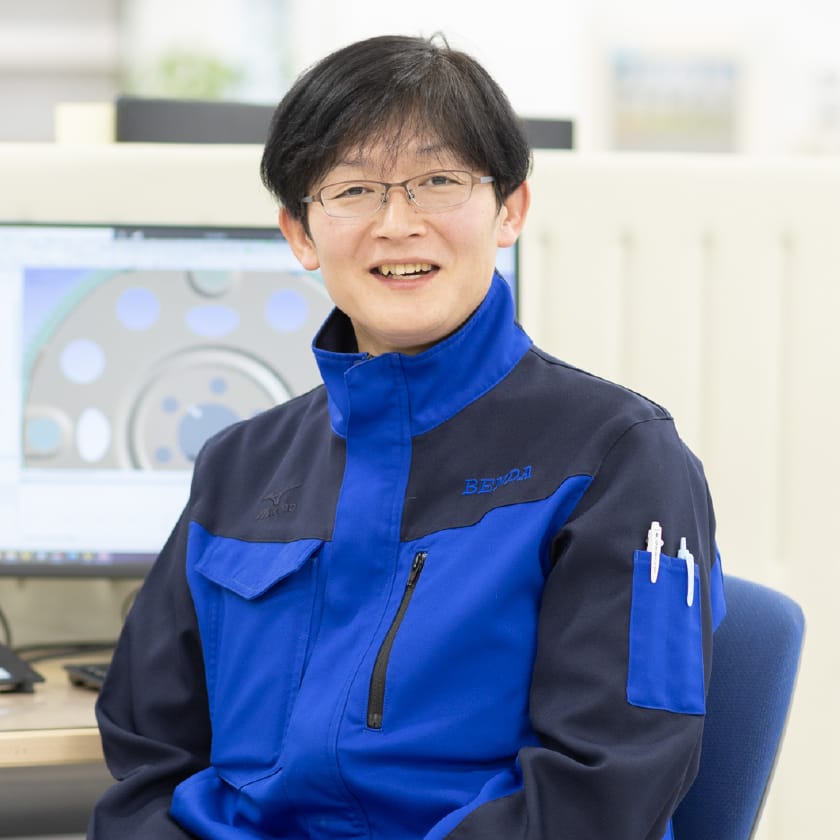
- Technology
Development
Department
Deputy General
Manager - Kazuhiko
Katayama - Joined the company in 2003
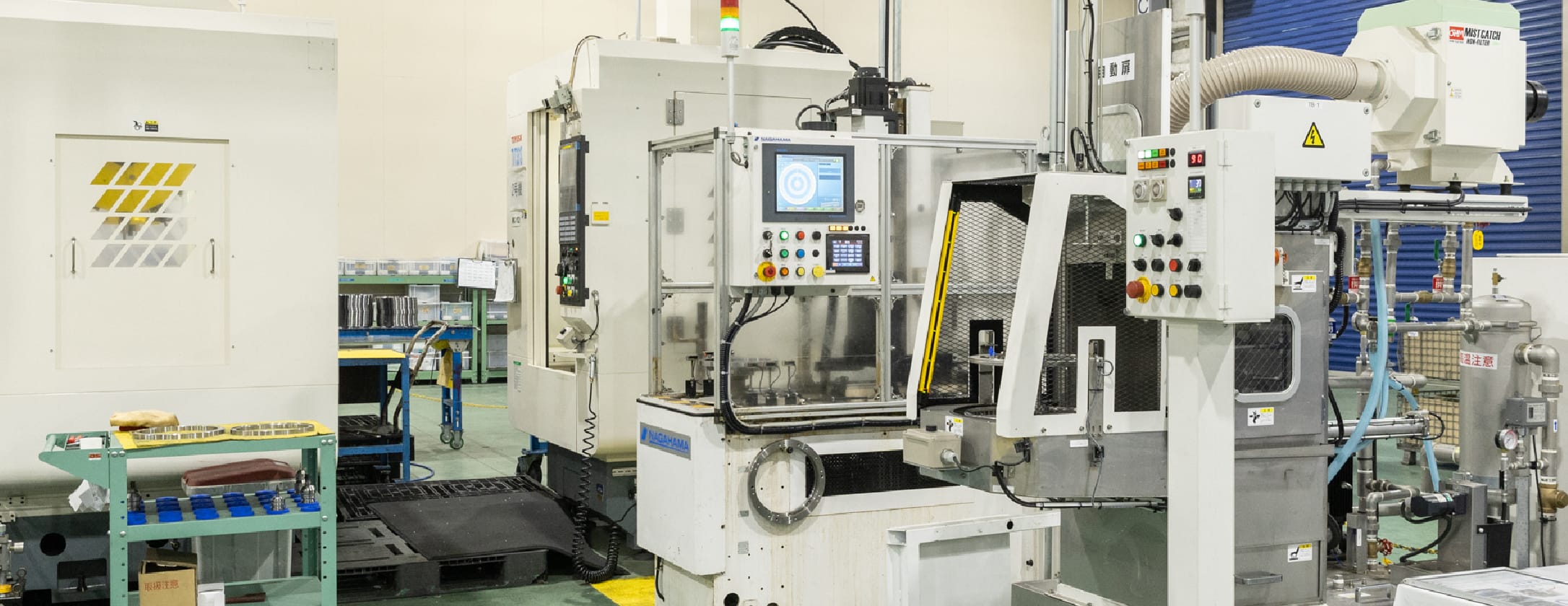
Mission:Develop a small cross-sectional ring!
The Benda Group has ascended to the status of a global Tier 1 supplier through its Benda method.
Maintaining this position in the rapidly changing global market is not easy.
With the era's shifts, exemplified by CASE (Connected, Autonomous, Shared, Electric),
a transition from internal combustion engine products to electrified products is anticipated.
The challenge for the engineers who will carry the next generation, inheriting the Benda spirit, has begun.
Future Market Demand
The Benda Group's main products are for internal combustion engines in automobiles. In the third medium-term management plan "NEXT" formulated in 2021, it was predicted that the demand for internal combustion engines would peak out in 2030. Therefore, a goal was set to gradually increase the proportion of electrified products and future products. It was thought that the highly sustainable production technology cultivated through the Benda method could be applied not only to ring gears but also to ring products incorporated into various industrial products.
As a stepping stone, we began mass production of "mass rings" used in hybrid vehicles. This move required significant capital investment, distinct from previous manufacturing processes, but the automated production line at the head office factory ensured a smooth supply.
Thus, the first step of a new product, which would become a pillar of our main product line, was taken, but this is merely the beginning. We should consider that the predicted peak out has already arrived. The next target is to develop products for electric vehicles (EVs). For future products, which have entirely different shapes and required functions compared to engine parts, the challenge for engineers has begun.
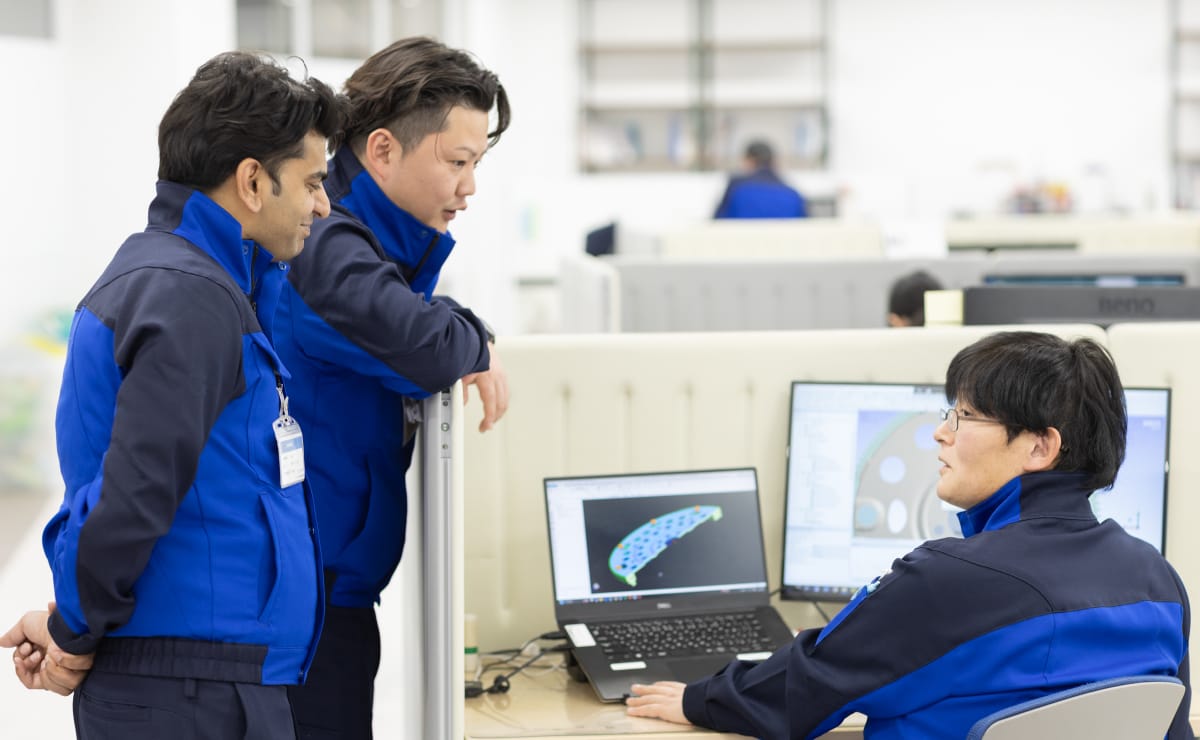

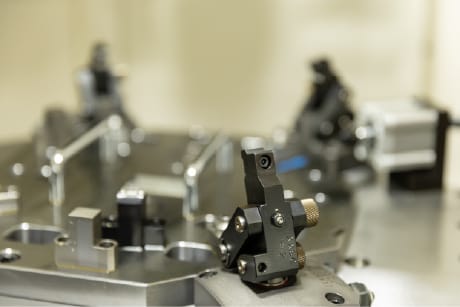
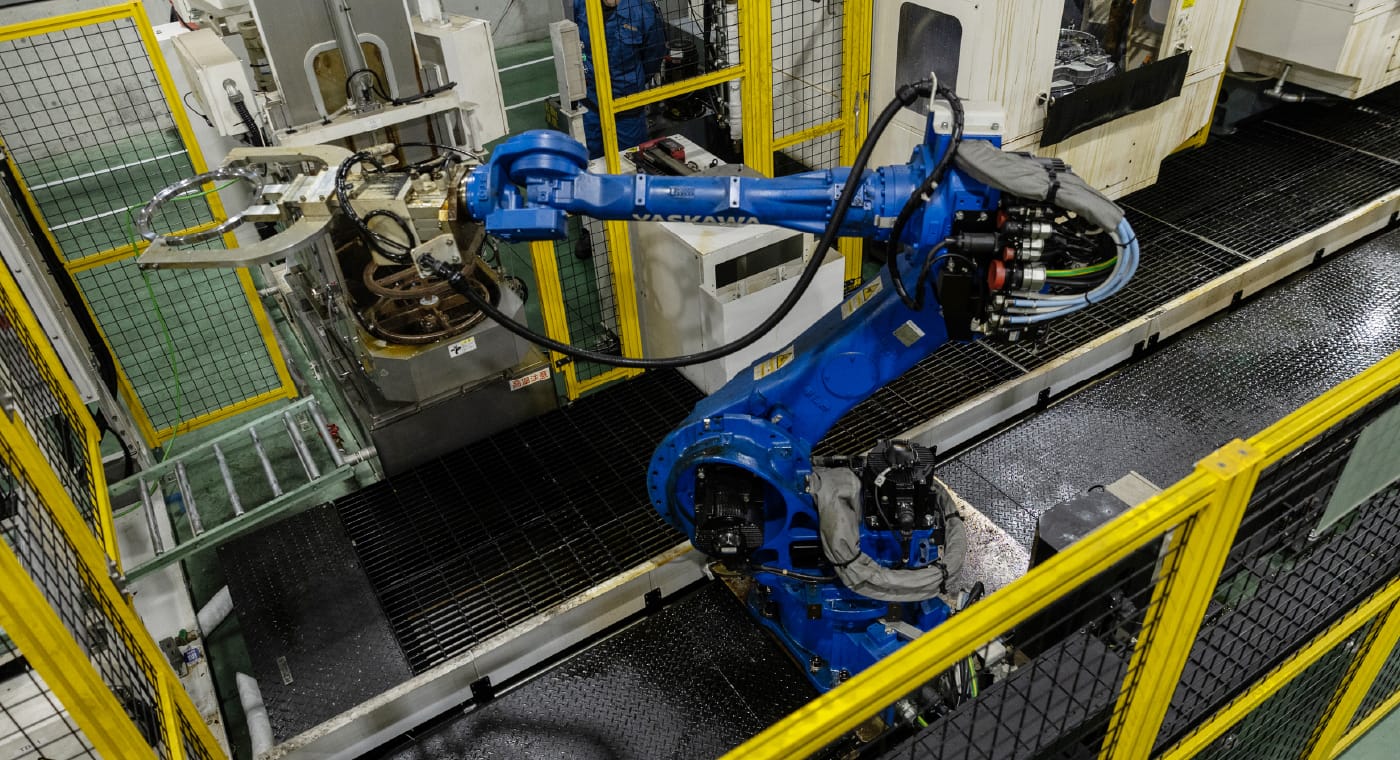
Head Office Kure Factory: Mass Ring Production Line
At our head office Kure factory, we have established a mass production system for the 'mass ring for hybrid dampers,' a new product for current electrified vehicles. As of the startup in April 2020, we achieved stable mass production of 20,000 units per month.
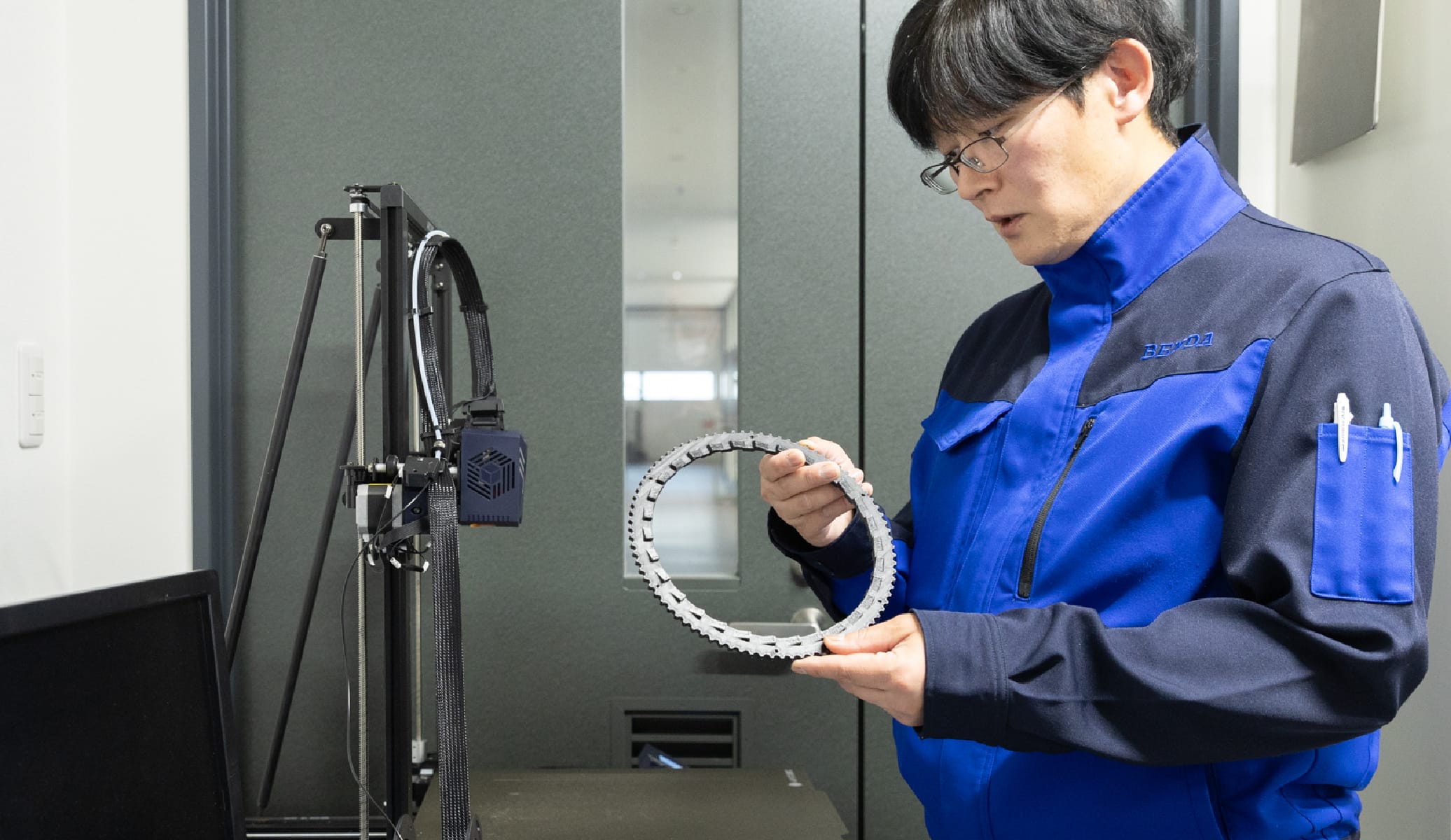
Development of EV Components:
Small Cross-sectional Rings
The mission entrusted to the engineers thus became something that would determine the future of the Benda Group. Among EV components, potentioal was found in the 'small cross-sectional rings,' for drive units. Miniaturization of parts is not limited to EVs; even in engines, miniaturization and weight reduction are progressing, so this was an unavoidable issue.
Kazuhiko Katayama (Deputy General Manager, Technology Development Department), who focuses on design, first tackled the NC conversion of the ring forming process. Previously, if the cross-sectional area was below a certain level, an additional machining process was required after ring forming, leading to increased material input and costs, making it difficult to receive orders for small cross-sectional ring products. Although these sizes had not been handled before, the possibility of producing them using the Benda method through the NC conversion of challenging processes led to design and prototyping efforts within the Technology Development Department.
Small cross-section rings have a much smaller cross-sectional area than existing products, and the durability of thin wire rods compared to rolled materials against 'bending,' as well as the work in each process such as cutting, welding, and heat treatment, needs to be reviewed. The first step was the technical development of 'bending, cutting, and welding,' which are the first half of the ring forming process. Through data analysis, the work that previously relied on the skills of experienced workers was successfully converted to NC.
In future development, we will work on the processes after welding, and the challenge towards mass production will begin.
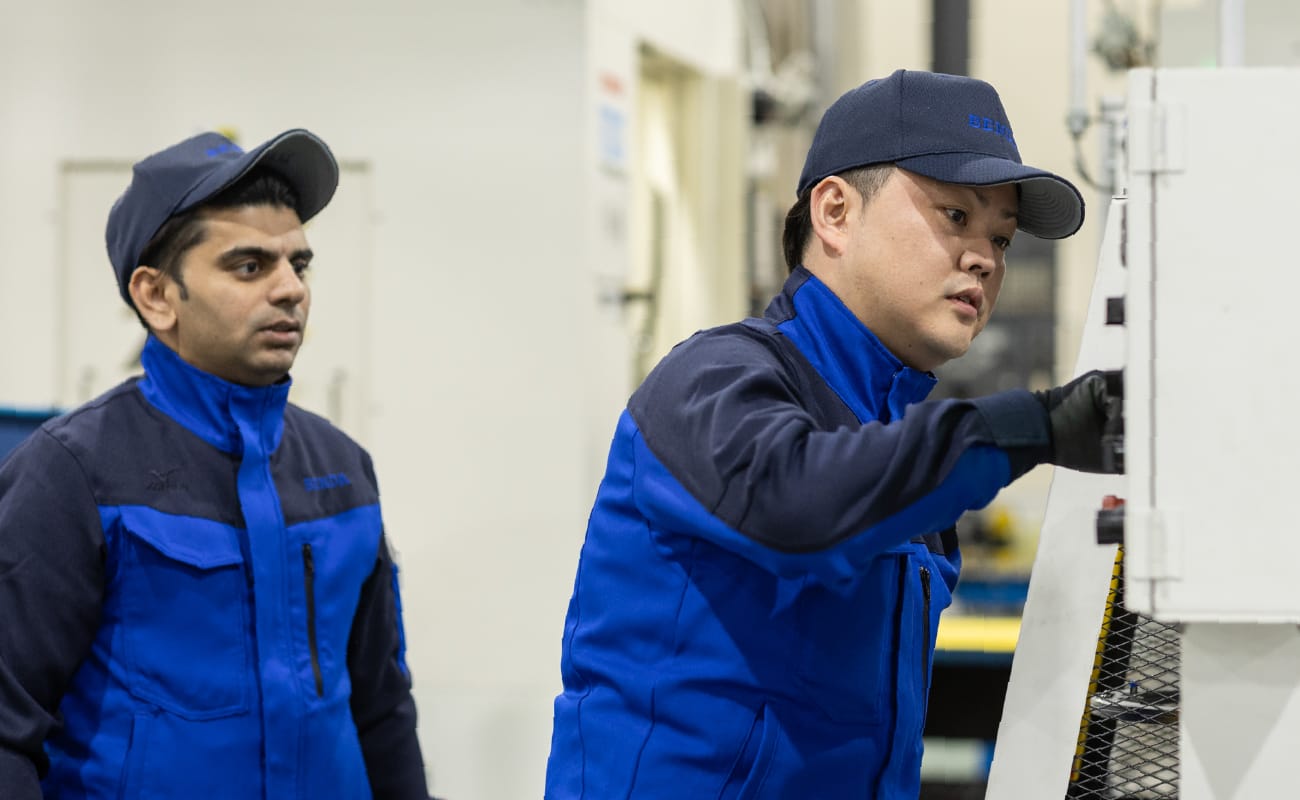
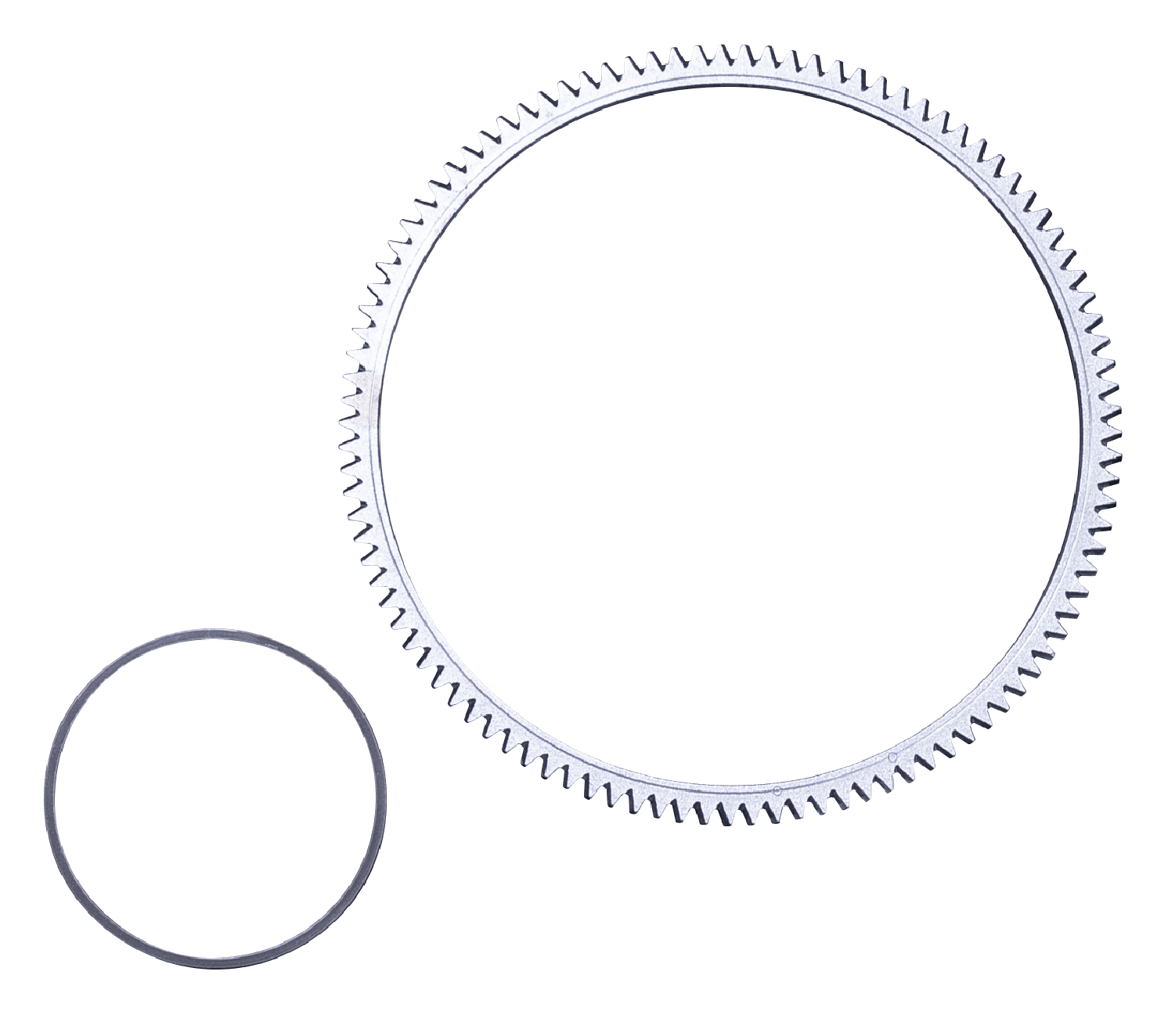
Small cross-sectional ring (left)
Comparison with existing product:
ring gear (right)